2025 Autor: Howard Calhoun | [email protected]. E modifikuara e fundit: 2025-01-24 13:25
Hedhja në kallëpe të guaskës quhet gjithashtu derdhja e guaskës. Dhe jashtë vendit, kjo metodë e punës quhet Shell.
Informacion i përgjithshëm
Në industrinë e sotme industriale, përdoren shumë metoda të ndryshme derdhjeje. Përveç derdhjes së guaskës, përdoret edhe derdhja investuese, si dhe në kallëpe metalike dhe disa metoda të tjera. Avantazhi i përgjithshëm i këtyre metodave të derdhjes, kur krahasohet me formimin me rërë, është se ato rezultojnë në materiale fundore më të sakta për sa i përket formës dhe dimensioneve. Për më tepër, numri i vrazhdësive në sipërfaqen e produkteve të tilla zvogëlohet. Në raste më të rralla, por megjithatë ndodh që nevoja për përpunim të mëvonshëm pas shkrirjes eliminohet. Përveç gjithçkaje, përdorimi i derdhjes në kallëpe guaskë dhe metoda të tjera kontribuon në faktin që ky proces të mund të mekanizohet sa më shumë që të jetë e mundur, si rezultat i të cilit rritet edhe automatizimi i tij. Dhe kjo, sigurisht, rrit shumë produktivitetin e çdo objekti industrial.
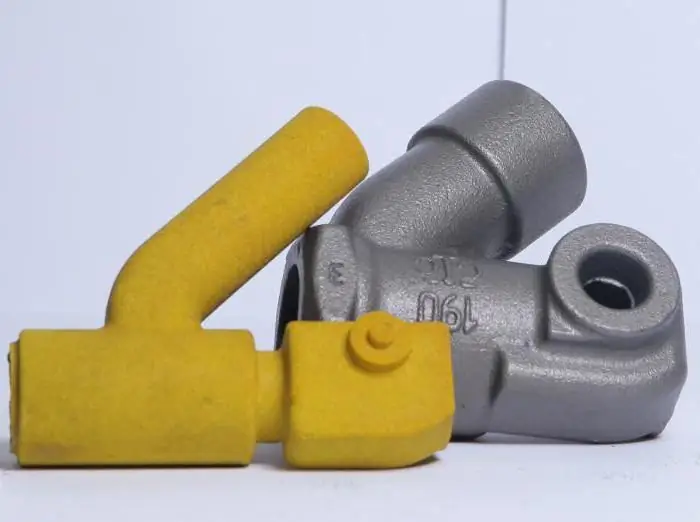
Shell casting
Nëse flasim konkretisht për këtëmetodë, ajo u prezantua për herë të parë në fabrika në vitin 1953. Aktualisht, metoda përdoret mjaft gjerësisht. Është derdhja në kallëpe të guaskës, për shembull, ajo që prodhon shumicën e pjesëve për traktorin Kirovets. Të gjitha pjesët që prodhohen duke përdorur këtë metodë janë të cilësisë më të lartë prej çeliku ose gize. Derdhja e guaskës është një metodë në të cilën rezultati përfundimtar i derdhjes ka një formë të përbërë nga dy predha rërë-rrëshirë. Gjithashtu, kjo metodë e prodhimit të pjesëve përdoret vetëm në rastet kur është e nevojshme të krijohet një pjesë me përmasa të vogla ose të mesme, por në të njëjtën kohë me saktësi të lartë. Shembuj aplikimesh për këtë metodë derdhjeje janë pjesët e motorit ose derdhjet me mure të hollë.
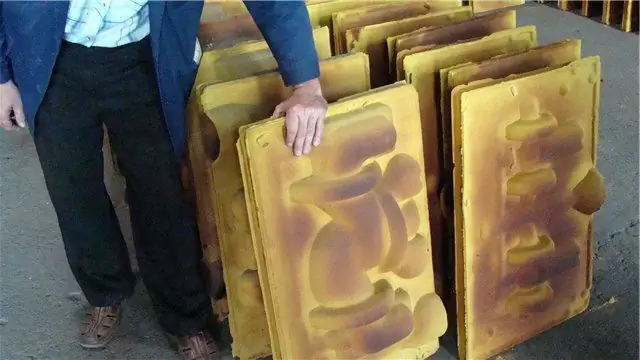
Thelbi i Rrugës
Me këtë metodë pune mund të merrni pjesë të ndryshme për ventilatorë, motorë, pompa apo makineri tekstili. Megjithatë, gjatësia maksimale e produktit të marrë nuk mund të kalojë 1 metër dhe nuk mund të jetë më e rëndë se 200 kg.
Esenca e derdhjes në kallëpe të guaskës bazohet në disa veti të rrëshirave termofikse, të cilat janë pjesë e përzierjeve rërë-rrëshirë. Avantazhi i përdorimit të komponentëve të tillë është se këto rrëshira priren të ngurtësohen shpejt dhe përgjithmonë kur trajtohen me një temperaturë prej 200-250 gradë Celsius.
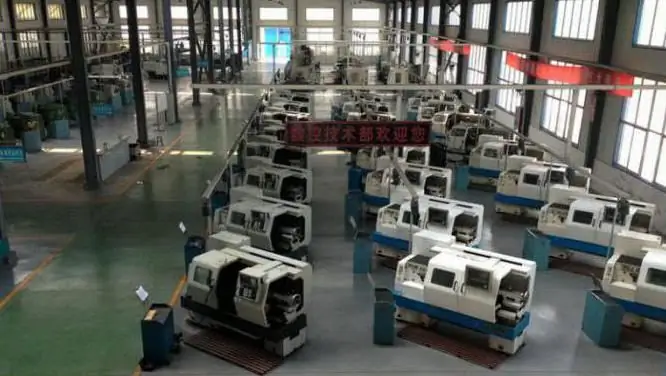
Bërja e një kallëpi me guaskë për derdhje
Për të bërë një kallëp për derdhjen e mëvonshme, është e nevojshme të kemi rërë kuarci me kokërr të imët, e cila vjen me shtimin e një rrëshirë termofikse, e cila është elementi i saj lidhës për të marrë një kallëp të plotë të guaskës. Këto materiale, në veçanti rrëshira, zgjidhen sepse ngurtësohen kur kalojnë një pengesë të caktuar të temperaturës. Procesi i prodhimit është si më poshtë. Së pari, rrëshira nxehet në 140-160 gradë Celsius. Nën ndikimin e një mjedisi të tillë, ai kthehet në një masë ngjitëse të lëngshme që mbështjell plotësisht mykun e rërës kuarci.
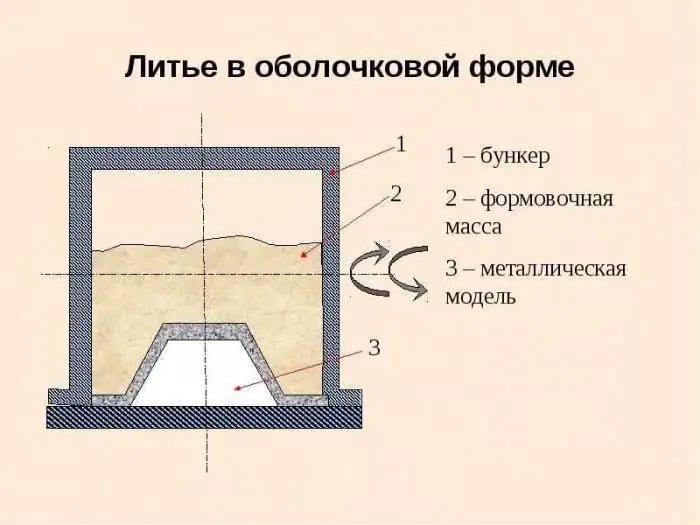
Fusha e derdhjes në kallëpet e guaskës është mjaft e gjerë, dhe për këtë arsye procesi i prodhimit të kallëpeve është sjellë në automatik ose automatik.
Pasi kallëpi është mbuluar plotësisht me rrëshirë, temperatura rritet në 200-250 gradë Celsius. Ky prag i temperaturës është mjaft i mjaftueshëm që masa ngjitëse të ngurtësohet në mënyrë të pakthyeshme dhe të formojë një formë. Më tej, kur fillon procesi i derdhjes së pjesëve, domethënë kur metali i shkrirë hyn në kallëp, temperatura në të arrin rreth 600 gradë. Kjo mënyrë është e mjaftueshme për të siguruar që rrëshira të mos shkrihet, por të digjet, duke lënë pore në vetë mykun, duke lehtësuar daljen e gazrave.
Përparësitë dhe disavantazhet e derdhjes së mykut me guaskë
Ashtu si çdo proces tjetër prodhimi, ky ka të mirat dhe të këqijat e tij. Nëse e krahasojmë këtë metodë të derdhjes, për shembull, me derdhjenkallëpe të zakonshme rëre, ka disa përparësi:
- Dallimi i parë dhe mjaft domethënës është klasa e saktësisë, e cila është 7-9. Për më tepër, përfundimi i sipërfaqes së pjesës së fituar përmirësohet deri në 3-6. Përveç kësaj, zvogëlohen lejimet, të cilat lejohen për përpunimin e mëvonshëm të pjesës që rezulton pas derdhjes.
- Një nga pluset e mëdha është një reduktim i ndjeshëm i kostove të punës për prodhimin e kallëpeve.
- Kjo metodë derdhjeje zvogëlon konsumin e materialeve të derdhjes, si dhe sasinë e metalit për faktin se madhësia e kanaleve të portës është zvogëluar.
- Zvogëloi ndjeshëm sasinë e prodhimit të martesës.
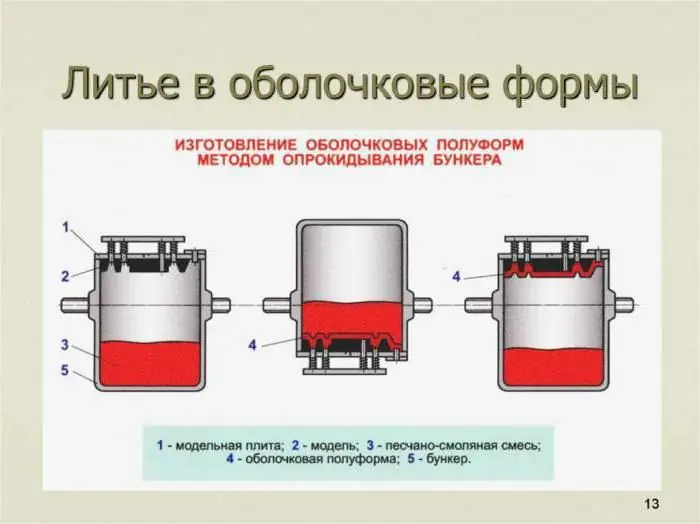
Megjithatë, ka disa disavantazhe të derdhjes në kallëpet e guaskës. Këto përfshijnë:
- Jeta e mykut të guaskës - 1 derdhje.
- Kostoja e formimit të rërës është mjaft e lartë.
- Përqindje e lartë e gazrave të dëmshëm.
Procesi i formimit të korpusit
Procesi i formimit të trupit kryhet në gjashtë faza:
- Hapi i parë është procesi i derdhjes së përzierjes në një model metalik të nxehtë, si dhe procesi i mbajtjes së tij për disa dhjetëra sekonda derisa të krijohet një kore e hollë dhe e fortë rreth pjesës. Më shpesh modelet janë prej gize dhe ngrohja e tyre kryhet deri në 230-315 gradë.
- Pas kësaj, është e nevojshme të kryhet një operacion për të hequr rërën e tepërt të derdhur. Trashësia e kores përfundimisht duhet të jetë nga 10 në 20mm. Kjo varet nga koha e qëndrimit të përzierjes në model, si dhe nga temperatura.
- Pas kësaj, pjata model së bashku me kallëpin duhet të transferohet në furrë, ku do të jenë deri në fund të procesit të pjekjes. Në fund të kësaj procedure, forca e guaskës duhet të jetë ndërmjet 2,4 dhe 3,1 MPa.
- Pasi hiqet nga furra, guaska e ngurtësuar zhvendoset nga pllaka. Për këtë procedurë përdoret një shtytës special.
- Pas kësaj, dy ose më shumë modele fiksohen së bashku duke përdorur një lloj kapëseje ose me ngjitje. Këto kallëpe mund të përdoren për derdhje në kallëpe guacke ose thjesht të ruhen. Jetëgjatësia pothuajse e pakufizuar.
- Para fillimit të procesit të derdhjes në kallëpin e përfunduar, në to hidhet e shtëna, e cila ndihmon në parandalimin ose shkatërrimin e mykut gjatë derdhjes së mëtejshme.
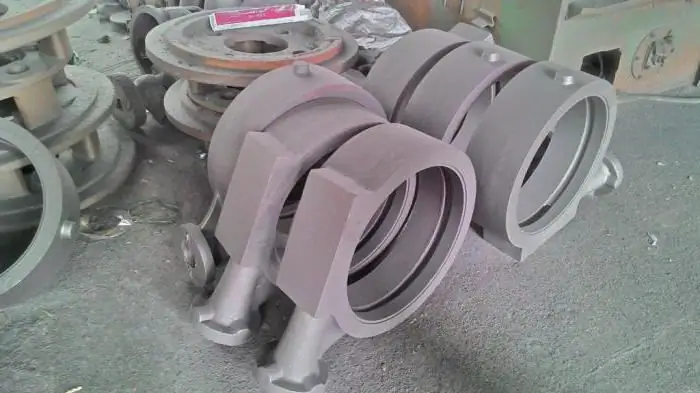
Detajet e transmetimit
Vlen të fillohet me faktin se tolerancat tipike që lejohen në prodhimin e veglave mund të jenë 0,5 mm. Vrazhdësia e sipërfaqes lejohet në rangun nga 0.3 në 0.4 mikron. Kufijtë e tillë justifikohen me faktin se përdoret rërë e imët. Gjithashtu vlen të theksohet: përdorimi i rrëshirës kontribuon shumë në faktin se sipërfaqja është shumë e lëmuar.
Vëllimet e prodhimit
Për t'u angazhuar në prodhimin e kallëpeve dhe pjesëve të tilla, është e nevojshme t'i kushtoni vëmendje instalimit të një modeli kallëpi. Koha e nevojshme për instalim është më pak se një javë. Pas përfundimit të instalimit, sasia e daljes mundarrijnë nga 5 deri në 50 copë në orë. Vëllime të tilla prodhimi në orë janë mjaft reale, megjithatë, për këtë është e nevojshme të përgatitet procesi i derdhjes në përputhje me rrethanat. Materialet kryesore që do të kërkohen për derdhje janë giza, alumini, bakri, si dhe lidhjet e këtyre llojeve të metaleve. Një material tjetër i nevojshëm do të jetë një aliazh që përdor alumin dhe magnez.
Recommended:
Sistemet e prodhimit dhe prodhimit: koncepti, modelet dhe llojet e tyre
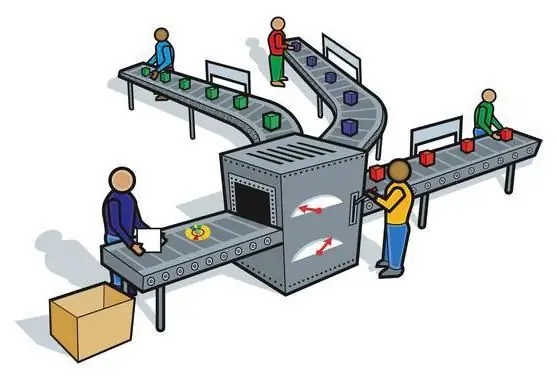
Sistemet e prodhimit janë struktura që përfshijnë njerëz dhe pajisje që punojnë së bashku. Ata i kryejnë funksionet e tyre në një hapësirë, kushte, mjedis pune të caktuar në përputhje me detyrat
Prodhim modern. Struktura e prodhimit modern. Problemet e prodhimit modern

Industria e zhvilluar dhe niveli i lartë i ekonomisë së vendit janë faktorë kyç që ndikojnë në pasurinë dhe mirëqenien e njerëzve të tij. Një shtet i tillë ka mundësi dhe potencial të madh ekonomik. Një komponent i rëndësishëm i ekonomisë së shumë vendeve është prodhimi
Metodat për llogaritjen e kostos së prodhimit. Kostot fikse për njësi të prodhimit
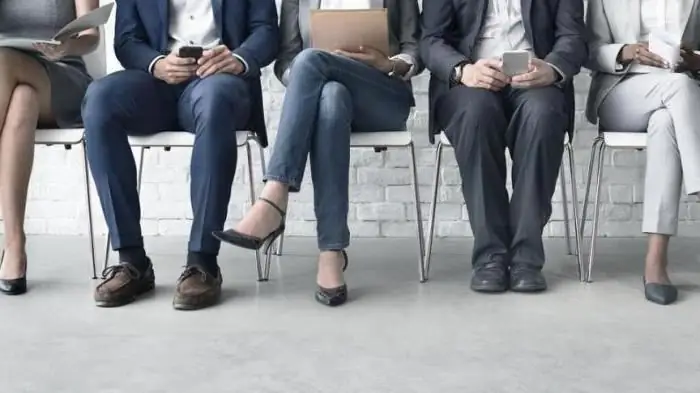
Kosto e prodhimit është një tregues i rëndësishëm ekonomik që pasqyron efikasitetin e aktiviteteve prodhuese. Prandaj, është kaq e rëndësishme që të jeni në gjendje të kryeni saktë llogaritjet dhe të nxirrni përfundime të arsyeshme. Le të shqyrtojmë më në detaje llojet kryesore, metodat e llogaritjes
Plani i biznesit të prodhimit të polisterolit: hapat hap pas hapi, teknologjia e prodhimit, llogaritja e të ardhurave dhe shpenzimeve
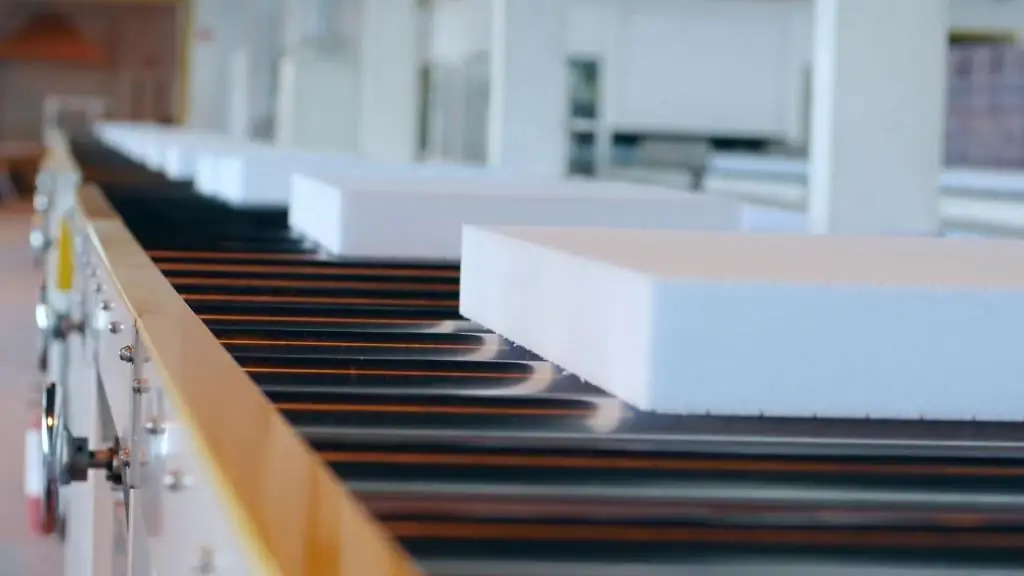
Polyfoam mund t'i atribuohet një prej materialeve ndërtimore më të përdorura. Kërkesa për të është mjaft e lartë, pasi ka një zhvillim të tregjeve të shitjeve, të cilat me një qasje marketingu kompetente mund të sigurojnë fitime të qëndrueshme për një periudhë të gjatë kohore. Në këtë artikull, ne do të shqyrtojmë në detaje planin e biznesit për prodhimin e plastikës me shkumë
Bankë tregtare. Funksionet dhe operacionet bazë
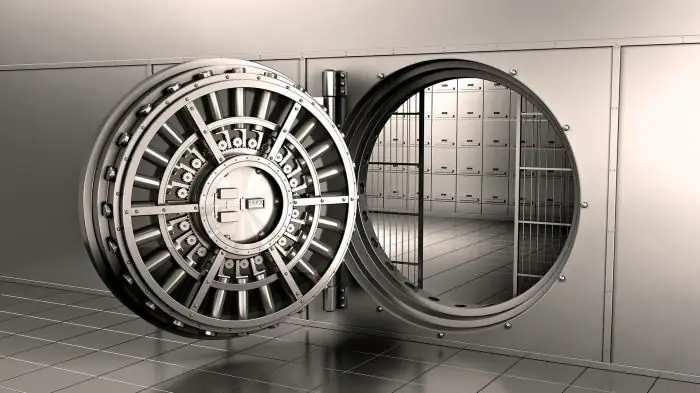
Një hallkë e rëndësishme në sistemin bankar është një bankë tregtare. Funksionet dhe operacionet kryesore të kësaj organizate kanë për qëllim marrjen e shumës maksimale të fitimit